※ Hình minh họa: Icarus trong thần thoại Hy Lạp và giấc mơ bay đến mặt trời (Nguồn: thechickenhawk)
Sau chiến tranh không lâu, câu khích lệ “Hãy đuổi kịp Mỹ trong vòng 3 năm” của cha đẻ của ngành sản xuất ô tô quốc nội Toyoda Kiichiro đã trở thành mục tiêu cụ thể của Toyota. Đã có mục tiêu cụ thể thì hành động của con người cũng trở nên hoạt bát hơn. Xí nghiệp cũng tương tự như vậy. Vào năm 1943, trong lúc còn chiến tranh, tôi đã chuyển chỗ làm từ nhà máy dệt sang sản xuất ô tô nhưng những kinh nghiệm có được từ thời ở nhà máy dệt đã trở nên rất có ích. Ý tưởng “Tự lao động hoá” mà đã được đề cập đến cũng được xuất phát từ chiếc máy kéo sợi “tự lao động” của ông Toyoda Sakichi, khi mới sang công trường sản xuất ô tô thì cũng là dân không chuyên về ô tô nhưng khi so sánh với bên kéo sợi thì tôi cũng nhận ra được nhièu ưu khuyết điểm của công trường.
Năm 1949, 1950 là thời kỳ phục hưng sau chiến tranh và cũng chính là lúc tiền đồ của ngành sản xuất ô tô Nhật Bản khá mờ mịt. Thêm nữa, nhìn vào số lượng sản xuất ô tô vào năm 1949, xe tải 25622 chiếc, còn xe hơi thì không quá 1008 chiếc, ngoài ra còn có 44118 chiếc xe tải được quân chiếm đóng bán ra nhưng xét cho cùng sản xuất trong nước vẫn là thiểu số. Mặc dù vậy, tại công trường sản xuất của Toyota thì lại có một khí thế như là cần phải làm một điều gì đó. Câu nói của Tổng giám đốc Toyoda Kiichiro không chừng cũng được nói ra trong bầu không khí như vậy.
Năm 1947, tại công trường chính thuộc thị trấn Toyota (vào lúc đó được gọi là công trường Koromo), chủ nhiệm công trường máy móc số hai lúc đó là tôi đã nghĩ ra ý tưởng để có thể đuổi kịp Mỹ thì một người không chỉ tác nghiệp cho 1 máy mà cần phải đảm nhiệm nhiều máy và nhiều công đoạn. Để có thể biến điều đó thành hiện thực thì tôi đã bắt đầu suy nghĩ và nhận ra rằng cần thiết phải tạo ra được quy trình hoàn chỉnh cho công trường máy. Tại các công trường ở Mỹ cũng như hầu hết các công trường ở Nhật, nói đến công trường máy thì khu máy tiện không được sử dụng vào bất cứ mục đích nào khác ngoài tiện. Cả cách bố trí công xưởng cũng không hiếm trường hợp sắp xếp 50, 100 chiếc máy tiện ở chung một chỗ. Sau khi xong công đoạn tiện thì gom lại và chuyển sang công đoạn khoan lỗ tiếp theo đó. Hoàn tất xong thì lại cũng như vậy tiếp tục gom lại chuyển sang công đoạn phay. Đây được cho là “quy trình tác nghiệp” từ trước đến nay. Trong trường hợp của Mỹ, một công ty bao gồm nhiều bộ phận có chức năng riêng biệt khác nhau. Do vậy, công trường tiện thì không làm gì khác ngoài tiện, còn cần khoan lỗ thì nhất thiết phải mang đến chỗ khoan. Mà mỗi nơi chỉ đảm nhiệm một chức năng nên đôi khi tại công đoạn tiện cần phải hàn một chút thì cũng không thể làm được, chỉ có thể mang ra chỗ hàn. Cho nên điều này cũng dẫn tới số lượng máy móc cũng như nhân công nhiều lên. Trong điều kiện như vậy mà phải giảm giá thành thì các xí nghiệp Mỹ rõ ràng chỉ còn cách là sản xuất hàng loạt.
Dựa vào việc tăng lượng sản xuất, giảm chi phí nhân công cho mỗi sản phẩm làm ra và làm nhẹ bớt đi chi phí bồi thường. Nếu như vậy thì nhất thiết phải cần một chiếc máy lớn có tính năng cao và tốc độ nhanh. Hệ thống sản xuất như vậy gọi là hệ thống lượng sản kế hoạch (kế hoạch sản xuất với số lượng lớn). Tại mọi công đoạn đều sản xuất thật nhiều sau đó gom lại và chuyển sang công đoạn tiếp theo. Đương nhiên là cách thức theo đuổi tốc độ và số lượng như vậy sẽ dẫn tới nhiều lãng phí. Cứ mãi theo đuổi phương thức kiểu Mỹ nên cho tới tận cuộc khủng hoảng dầu mỏ vào năm 1973, các doanh nghiệp Nhật Bản vẫn ảo tưởng rằng phương thức này hoàn toàn phù hợp với phong thổ Nhật Bản.
Tạo dựng nên quy trình sản xuất
Để có thể phá bỏ được tính bảo thủ của công trường máy, rằng tiện chỉ có thể làm ở công trường tiện hay hàn chỉ có thể làm ở khu hàn, quả thật không phải điều dễ dàng. Tại Mỹ thì không có khả năng nhưng nếu ở Nhật thì chỉ cần có quyết tâm thì có thể được. Thật ra, việc bắt đầu phương thức sản xuất Toyota chính là bắt đầu khiêu chiến với cái tôi hướng về thể chế cũ.
Năm 1950, chiến tranh Triều Tiên bùng phát, nhờ đó kinh tế Nhật đã khởi sắc trở lại nhờ sản xuất các đặc nhu yếu phẩm. Và ngành sản xuất ô tô cũng cưỡi lên con sóng đó mà phát triển lên. Năm này cũng là năm rất bận rộn đối với Toyota. Cùng với việc cắt giảm nhân công từ tháng tư đến tháng sáu dẫn đến kháng nghị lao động và hậu quả là Tổng giám đốc công ty ông Toyoda Kiichiro đã nhận trách nhiệm và từ chức. Sau đó thì cuộc chiến Triều Tiên nổ ra.
Dẫu là sản xuất hàng đặc yếu phẩm nhưng vẫn khác xa so với lượng sản. Chính là ở chỗ nhiều chủng loại. Không khác gì so với sản xuất đa chủng thiểu lượng. Tôi thì lúc đó với tư cách trưởng công trường máy tại công trường Koromo đã thay đổi cách bố trí thiết bị máy móc, thay đổi luôn cách làm từ trước đến giờ làm gom lại gia công thật nhiều rôi chuyển sang công đoạn tiếp theo thành cách đặt liên tiếp các máy khác nhau theo thứ tự gia công và sản xuất từng cái từng cái một, bắt đầu thử nghiệm quy mô nhỏ để tạo ra một quy trình sản xuất mới. Năm 1947, thử nghiệm sắp xếp máy theo hình chữ nhị (二) hay chữ L và mỗi người tác nghiệp phụ trách 2 chiếc. Từ năm 1949 đến 1950 thì sắp xếp theo hình chữ “コ“ hay hình chữ “ロ”, mỗi người thử phụ trách từ 3 đến 4 chiếc. Tất nhiên trong công trường sản xuất cũng xuất hiện nhiều kháng nghị. Chẳng phải là do lượng công việc hay thời gian tác nghiệp tăng lên hay gì mà là do mọi người đều là công nhân chuyên ngành tốt xấu gì cũng mang đậm chất thợ nghề nên khi đổi cách sắp xếp máy móc thì phải chuyển cách làm từ trước đến giờ là đảm nhiệm một máy sang nhiều máy theo thứ tự công đoạn từ tiện sang phay đến khoan,… công việc đòi hỏi công nhân phải biết nhiều tính năng, dẫn đến phản kháng cũng là chuyện đương nhiên. Với lại thực tế bắt tay vào việc mới phát hiện ra nhiều vấn đề. Ví dụ như là máy đã hoàn tất gia công mà không chịu dừng lại hay là do cần phải điều chỉnh nhiều mà lại không quen dẫn đến khó sử dụng. Tất cả những vấn đề từ từ lộ ra và chỉ cho tôi thấy con đường tiếp theo nên đi là gì. Tôi vẫn còn trẻ, tràn đầy nhiệt huyết nên cố áp đặt thay đổi lớn trong thời gian ngắn cũng không phải là cách hay, không cần vội vã, gấp gáp mà cứ từ từ chậm rãi.
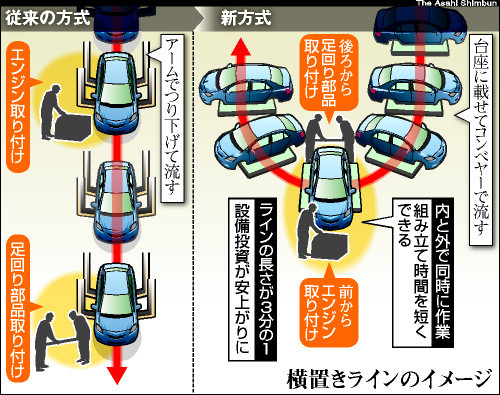
Theo cuốn トヨタ生産方式 大野耐一
Dịch bởi: Trịnh Trần Khánh Duy