Công việc cần luôn luôn suy nghĩ “mục đích là gì?”, và không làm mờ nhạt nó. Phương pháp, cách làm để đạt được mục đích thì có vô số, nhưng nếu xác định rõ ràng “mục đích là gì?” thì sẽ tìm thấy được phương pháp, cách làm tốt nhất. Không được tìm kiếm mục đích bằng bộ não bị giới hạn cách làm, phương pháp.
Ông F, người đã tiến hành hoạt động kaizen khá dài ở Toyota đã chuyển sang làm công chức tại một hãng thực phẩm. Công ty này đang hướng đến cải cách sản xuất và tìm con đường đi theo phương thức của Toyota. Ông F rất giàu kinh nghiệm trong việc thực hiện cải cách sản xuất tại công ty hiệp lực của Toyota. Ông cũng có tự tin trong việc phát triển phương thức sản xuất của Toyota trong các lĩnh vực khác ngoài ô tô. Ông nghĩ rằng sẽ áp dụng được know how của bản thân trong lĩnh vực thực phẩm.
Tuy nhiên lại xảy ra bế tắc ngay tại thời điểm bắt đầu cải cách. “Kanban” (phiếu chỉ thị tác nghiệp, vận chuyển…) đã sử dụng quen thuộc lâu năm lại không được thông dụng. Kanban đã trở thành tiền đề cho bình chuẩn hóa sản xuất (bình quân hóa tổng hợp số lượng, chủng loại sản phẩm sản xuất)
Sản lượng sản xuất nếu bị chênh lệch lớn tùy theo ngày và thời gian thì việc kết hợp và chuẩn bị con người, thiết bị sẽ chất thành “núi”. Ngược lại, ngày và thời gian quá rảnh thì cả con người và máy móc để ở tình trạng “chơi”. Vì vậy trong phương thức Toyota, loại trừ lỗ hổng và lãng phí bằng cách suy nghĩ và tiến hành bình chuẩn hóa sản xuất. Và cũng nhờ đặt tại đó mà Kanban phát huy được hiệu quả.
Tuy nhiên, với thực phẩm, tùy theo ngày mà lượng bán được khác nhau. Đương nhiên, việc đặt hàng của siêu thị cũng có sự khác nhau rõ rệt tùy theo từng ngày. Nếu cứ cố gắng bình chuẩn hóa thì có thể dẫn đến tình trạng tồn kho. Nếu như vậy sẽ đi ngược lại với phương châm cung cấp thực phẩm tươi sống đến cho khách hàng. Công ty này phù hợp với cách làm giảm hàng tồn kho và sau khi nhận đơn hàng thì ngay lập tức chế biến rồi mang đến cho khách hàng.
Từ đó, ông F đã từ bỏ cách làm theo bình chuẩn hóa và Kanban, xây dựng dây chuyền sản xuất lấy suy nghĩ công đoạn sau làm cơ bản.
1.Thông thường… trước tiên, công đoạn trước chế biến, sau đó công đoạn sau tiếp tục tiếp nhận
2.Phương thức Toyota…Tùy theo mức độ cần thiết, công đoạn sau sẽ tiếp nhận từ công đoạn trước. Những chi tiết ứng dụng tại công ty sản xuất phần công đoạn trước đã tiếp nhận sẽ được bỏ qua. Sau khi thay thế bằng cách làm này, dây chuyền sản xuất đã hoạt động tốt hơn, dẫu lượng hàng bán được có bị biến động thì lợi nhuận vẫn sẽ tăng.
Tuân thủ cơ bản của suy nghĩ
Dẫu vậy, ông F cũng từng băn khoăn về việc không sử dụng Kanban. Trong khi phân vân “Thực sự cách làm này có ổn hay không?” thì ông Taiichi Ono đã ghé thăm để xem xét tình hình. Ông F đã đặt câu hỏi:
“Với trường hợp của thực phẩm, việc bình chuẩn hóa sản xuất là không thể, Kanban cũng không sử dụng được. Vì vậy, chỉ có thể sử dụng suy nghĩ tiếp nhận công việc của công đoạn sau mà thôi. Như vậy có ổn hay không?”
Ông Taiichi Ono đã trả lời rằng:
“Kanban đơn thuần cũng chỉ là một phương pháp. Làm theo cách tuân thủ cơ bản của suy nghĩ tiếp nhận công việc của công đoạn sau như hiện tại là ổn rồi.”
Điều đó đã tiếp thêm sức mạnh cho ông F.
Vì phương thức Toyota được gọi là “phương thức Kanban”, nên nhiều người hiểu nhầm nhờ có Kanban mới có được phương thức Toyota. Tuy nhiên, Kanban đơn thuần cũng chỉ là một phương pháp. Mục đích là “vừa nâng cao chất lượng sản phẩm, vừa cố gắng giảm chi phí sản xuất tối đa để tạo ra lợi nhuận”. Chính vì vậy mà tiến hành kaizen và loại bỏ lãng phí. Nếu quên mất điều cơ bản này và chỉ dựa vào Kanban thì nhiều trường hợp sẽ kết thúc bằng cải cách thất bại.
Trước đây, khi ông Ono đi thị sát công xưởng, có những công xưởng đã đưa ra Kanban rất hoành tráng tự mãn rằng chúng tôi đang “tiến hành cải cách”. Tuy nhiên, dẫu có tạo ra Kanban hoành tráng như thế nào thì cũng không mang lại ý nghĩa gì cả. Quan trọng hơn cả là “mục đích là gì?”. Nếu lẫn lộn Kanban đơn thuần chỉ là một phương pháp với mục đích thì chắc chắn không thể tiến hành cải cách được.
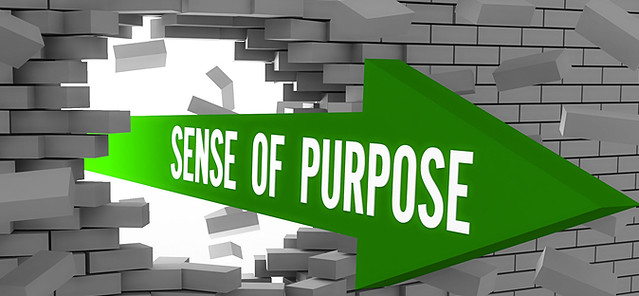
Những việc “lẫn lộn giữa phương pháp và mục đích” thường xuyên được nhìn thấy. Không thể tiêu diệt hoàn toàn những trường hợp hiểu sai “Vì đã tự động hóa, đã nhập robot, đã nhập máy tính nên thiết bị đã được rút ngắn thời gian làm việc, và văn phòng đã trở nên lý tưởng hơn”. Không được quên “làm vì điều gì?”. Cần luôn luôn để suy nghĩ “mục đích là gì?” trong đầu.
Kể cả hoạt động kaizen, cũng có trường hợp quên mất mục đích và cho việc kaizen trở thành mục đích. Một số người lãnh đạo hàng đầu, thay vì khuyến khích nhân viên cố gắng hết mình để tiến hành kaizen, lại rời xa mục đích “vì khách hàng”, “để giảm chi phí sản xuất” để hướng đến kaizen mà những người hàng đầu hứng thú. Nhìn qua các con số vẫn tăng, những “kaizen” xuất sắc thì trên con mắt tác giả đơn thuần chỉ là “kaizen ảo”, không đạt được mục đích thực sự.
Chắc chắn có người sẽ nghĩ rằng “Bản thân không thể nào làm những việc ngu ngốc như là vất bỏ mục đích được”. Tuy nhiên, suy nghĩ “chỉ có phương pháp, cách làm này thôi!” sẽ làm con người dễ đánh mất mục đích thực sự.
Biên dịch: Kiều Chinh
Theo cuốn: ”トヨタの上司は現場で何を伝えているのか”